...
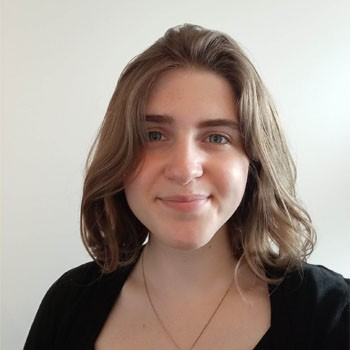
Written by Aurélie Tavernier
Marketing and Communications Manager at Immersive Factory.
She became interested in raising awareness of health and safety at work, convinced that an approach tailored to employees can transform the safety culture and reinforce shared vigilance. Her ambition: to encourage all companies, whatever their size, to invest actively in health and safety prevention for the well-being of their employees.